Yamaha Craftsmanship
A firmly imbedded spirit of craftsmanship can be found at the manufacturing and production facilities of Yamaha Motor. This craftsmanship is about adding on extra touches in each stage of the production process by calling on the sensitivities unique to our brand, the traditions of our manufacturing worksites, and the pride and special sense of each specialist at work. With Yamaha outboards, everything we do is to ensure we continue to deliver on our legendary reputation for producing the world’s most reliable outboard engines.
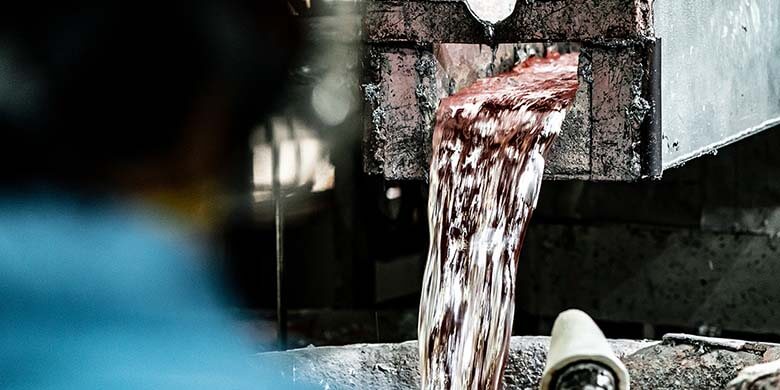
ALUMINIUM MELT PROCESS
If you trace back the various steps of the manufacturing process for building performance, functions, quality, and design into a product, everything begins with the raw materials used. And because delivering unquestionable reliability is the goal when producing Yamaha outboards, the first step in the production process is at aluminum smelting sites.
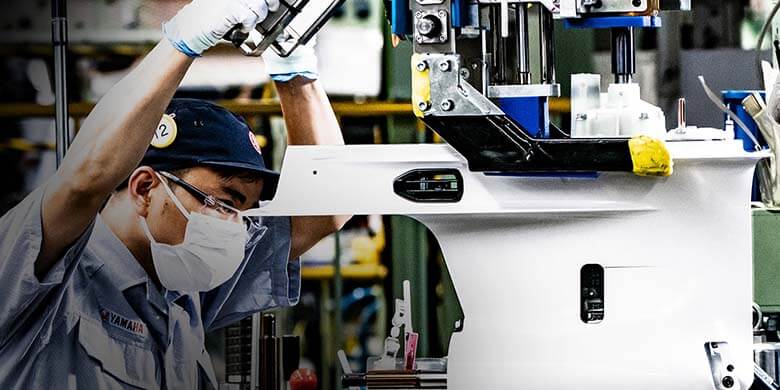
ALUMINIUM PART MANUFACTURING
The lower unit is the bottommost part of an outboard motor and is made from a single large aluminum casting. Its high resistance to corrosion while submerged in the harsh operating environment of the world‘s waters is the product of carefully selected materials, precision machining techniques, and the application of a proprietary undercoating using first-rate painting technologies.
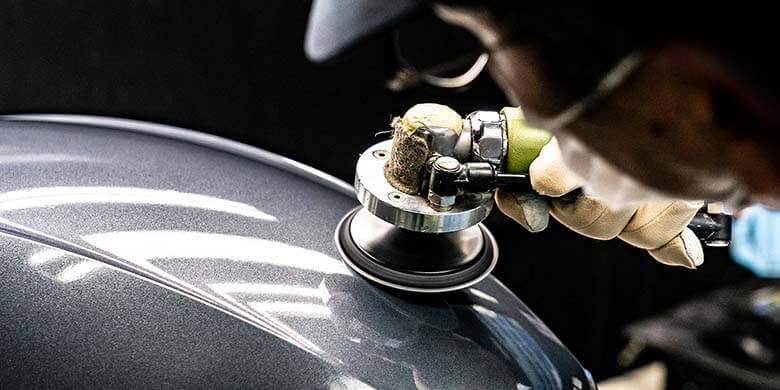
PLASTIC PART MANUFACTURING
The powerhead cowling envelops the outboard engine and it must be well engineered and functional to protect it from the water. But since it doubles as the “face” of the outboard, it must also sport a highly attractive and refined design. To enhance the natural beauty of the cowling’s curves and contours, Yamaha’s craftsmen bring their finely honed senses and skills to bear
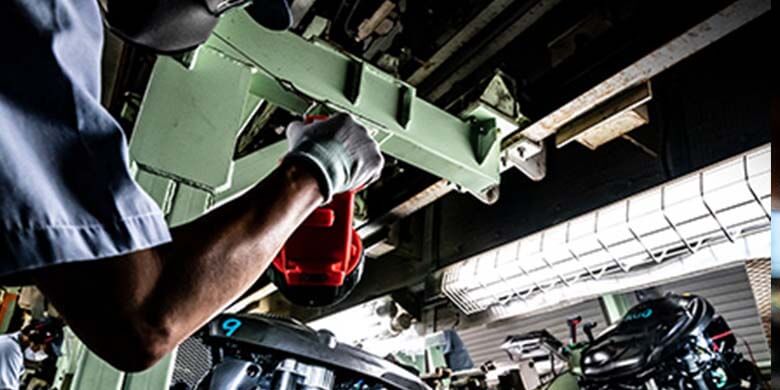
FINAL INSPECTION
At Yamaha’s outboard motor assembly factory is a series of large water tanks designed to simulate the open sea, and this is where newly completed engines are given their final tests and checks. Every Yamaha outboard engine – without exception – gets its baptism in one of these tanks with a full-throttle test run before being shipped out to countries and waters around the world.